Plastic extrusion for detailed profiles and custom designs
Plastic extrusion for detailed profiles and custom designs
Blog Article
Trick Benefits and Factors To Consider of Executing Plastic Extrusion in Your Projects

Recognizing the Fundamentals of Plastic Extrusion
Plastic extrusion, a staple in the production market, is a procedure that includes melting raw plastic material and reshaping it into a constant profile. This profile, once cooled down, can be reduced right into wanted lengths or coiled for later usage. The elegance of plastic extrusion depends on its adaptability. A wide variety of items, from piping to home window frameworks, can be created. The process requires an extruder, an elaborate device with a warmed barrel, a turning screw, and a die at the end. The plastic material, in the form of pellets, is fed right into the extruder, where it's melted and forced via the die, taking its shape. The selection of plastic and the layout of the die figure out the product's features.
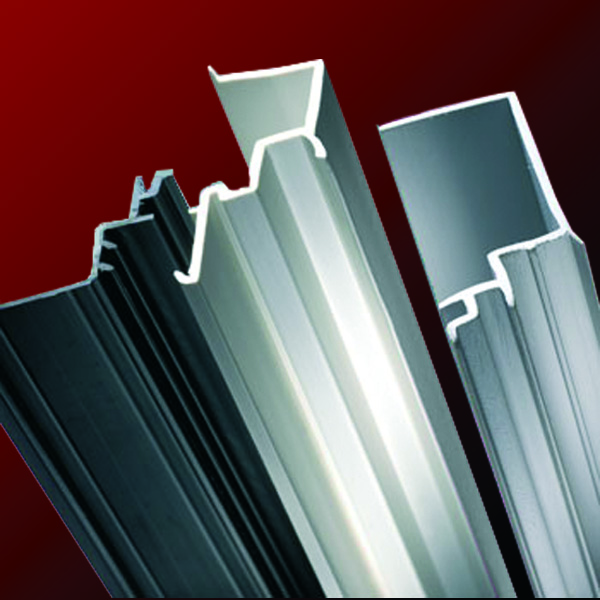
The Economic Benefit of Plastic Extrusion
The economic advantage of plastic extrusion lies predominantly in two locations: cost-effective product production and helpful manufacturing speeds. With plastic extrusion, services can produce high quantities of product at a lower expense compared to various other methods. The process boasts a remarkable production speed, substantially lowering time and more enhancing its economic practicality.
Cost-efficient Product Manufacturing
A significant benefit of plastic extrusion is its amazing cost-effectiveness. This production process enables continual, high-volume production with minimal waste, which translates right into lower costs. The raw materials used, normally plastic pellets, are fairly inexpensive compared to various other materials (plastic extrusion). The procedure itself calls for less energy than many other manufacturing methods, even more decreasing costs. Additionally, the extrusion procedure allows for a high level of accuracy fit the plastic, minimizing the demand for pricey post-production changes or improvements. Moreover, the durability and durability of extruded plastic products typically imply less require for replacements, adding to long-lasting cost savings. All these factors make plastic extrusion a very cost-effective choice for lots of jobs, using an eye-catching equilibrium between price and performance.
Beneficial Production Speeds
While maintaining the cost-effectiveness of the products, one more notable benefit of plastic extrusion exists in its quick production rates. This combination of quality, rate, and cost-effectiveness highlights the substantial economic benefit of implementing plastic extrusion in numerous tasks.
Convenience and Personalization: The Strengths of Plastic Extrusion
Among the noticeable staminas of plastic extrusion exists in its flexibility and customization potential. These qualities open up the door to unrestricted style opportunities, providing producers the ability to tailor products to specific demands. This increased level of customization not only boosts product functionality yet additionally significantly enhances product originality.
Unrestricted Style Possibilities
Plastic extrusion shines in its capacity to provide virtually infinite style opportunities. This method offers freedom to develop complicated shapes and detailed accounts, a task difficult to achieve with other manufacture methods. Owing to the fluid nature of liquified plastic, the process is adaptable enough to generate a diverse variety of types, dimensions, and dimensions. The plastic can be adjusted to match unique specs, enabling the production of personalized geometries and conference specific client demands. Plastic extrusion can manage a variety of plastic types, broadening its application extent. This versatile technique, therefore, serves a wide variety of industries from construction to auto, packaging to electronics, and beyond. With plastic extrusion, the style possibilities are basically endless.
Increasing Product Individuality
The flexibility of plastic extrusion can considerably boost item originality. This procedure enables designers to trying out different shapes, dimensions, and next page shades, providing the flexibility to create special products that stand apart out there. It is this personalization that offers an unique identification to each product, distinguishing it from its rivals.
Along with its visual advantages, the customizability of plastic extrusion likewise offers functional benefits. Designers can change the residential or commercial properties of the plastic according to the details needs of the application, boosting the item's capability. As an example, they can make the plastic a lot more flexible, more long lasting, or a lot more resistant to heat, relying on what the product calls for. Thus, plastic extrusion not just boosts product uniqueness but additionally its utility and bankability.
Style Limitations in Plastic Extrusion: What You Need to Know
Just how can create limitations potentially influence the process of plastic More Bonuses extrusion? While plastic extrusion is functional, style constraints can cut its benefits. Certain complex designs may not be practical due to the restrictions of the extrusion procedure, possibly restricting the creation of detailed profiles. The procedure is less ideal for hollow or multi-chambered structures. In addition, the extrusion procedure might not constantly offer the preferred surface coating, specifically for those requiring high gloss or optical clearness. Product option can likewise posture challenges, as not all polymers appropriate for extrusion. High-temperature resistant plastics, as an example, may provide problems. Recognizing these constraints is important for efficient execution of plastic extrusion in your tasks. plastic extrusion.
Assessing the Environmental Effect of Plastic Extrusion
While recognizing style limitations is a substantial element of plastic extrusion, it is just as essential to consider its ecological ramifications. The process of plastic extrusion includes melting plastic products, potentially launching damaging gases into the atmosphere. Using recycled plastic materials in the extrusion procedure can reduce environmental impact.

Instance Research: Successful Projects Utilizing Plastic Extrusion
Success stories in the area of plastic extrusion abound, demonstrating both the versatility and efficiency of this production procedure. plastic extrusion. One more successful case is the production of plastic film for product packaging and agriculture. These instances show plastic extrusion's crucial role in numerous industries, proving to its versatility, cost-effectiveness, and reputable output.
Conclusion
In verdict, plastic extrusion supplies a reliable and affordable method for creating complex forms with very little waste. While it offers countless advantages such as cost-effectiveness and flexibility, Clicking Here it's crucial to take into consideration potential layout restrictions and ecological results. Implementing biodegradable or recycled products can alleviate these concerns, boosting sustainability. Including plastic extrusion into tasks can cause effective results, as confirmed by many instance studies.
Plastic extrusion, a staple in the production industry, is a procedure that includes melting raw plastic material and reshaping it into a constant account. Plastic extrusion can deal with a selection of plastic kinds, expanding its application extent.How can make limitations possibly impact the procedure of plastic extrusion? The process of plastic extrusion includes melting plastic materials, potentially launching damaging gases into the atmosphere. Making use of recycled plastic products in the extrusion process can lower ecological impact.
Report this page